Trolley Identification Solution for Modern Distribution Centres
Posted on 23/05/2019 in New Product Launches, by Jon
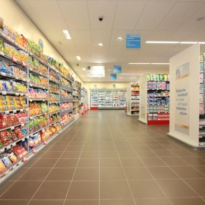
Trolley Identification Solution for Modern Distribution Centres
The Challenge
In today’s fast-paced retail environment, efficient logistics management is critical for operational success. One major retailer faced a significant challenge with their mesh trolley identification system:
- High-volume operations: Thousands of trolleys with rapid turnaround times between distribution centers and stores
- Time-consuming label removal: Traditional self-adhesive labels required complete removal before reuse
- Chemical dependency: Adhesive residue removal required harsh cleaning chemicals
- HACCP compliance concerns: Especially critical in food-handling environments where hygiene standards are strictly enforced
The Solution: Linerless Flag Labels
Soabar developed a custom solution combining innovative materials and specialized printing equipment:
- Linerless Technology: Replaced traditional adhesive labels with Sihl pressure TAC linerless material
- Adhesive activates only when folded and pressed together
- Label sticks to itself in a “flag” configuration, not to the trolley surface
- Eliminates adhesive residue on trolley surfaces
- Specialized Printing System: Soabar 6 Series printers designed specifically for this application
- Custom roller system for handling sensitive linerless materials
- Strategic print head positioning prevents material sticking to internal components
- Protected by optional MDF cabinet to withstand harsh distribution center environments
Benefits for Modern Operations
Case Study Example: A national grocery chain implemented this solution across 12 distribution centers, reducing trolley processing time by 68% and eliminating approximately 2 tons of backing paper waste annually.
Operational Improvements:
- ✅ Instant label removal: Labels pull off cleanly with no residue
- ✅ Chemical reduction: Eliminated need for adhesive-dissolving cleaning agents
- ✅ Extended run lengths: 50% more labels per roll compared to conventional materials
- ✅ Reduced downtime: Fewer material changes required during operation
- ✅ Waste reduction: No backing paper to dispose of
- ✅ Enhanced hygiene: HACCP compliant for food-safe environments
Sustainability Impact:
- 🌱 Minimized chemical use
- 🌱 Reduced paper waste
- 🌱 Lower disposal costs
- 🌱 Smaller carbon footprint from transportation (more labels per roll = fewer deliveries)
Real-World Implementation
Distribution centers have reported significant improvements after adopting this solution:
Metric | Before Implementation | After Implementation |
---|---|---|
Label removal time | 45-60 seconds per trolley | 5-10 seconds per trolley |
Chemical usage | 250L cleaning solution monthly | Minimal spot cleaning only |
Downtime for roll changes | 15-20 minutes, 3-4 times daily | 15-20 minutes, 1-2 times daily |
HACCP compliance issues | Frequent contamination concerns | Consistently compliant |
Next Steps
Discover how this innovative solution can transform your distribution center operations:
- Request an on-site demonstration
- Speak with our logistics solutions specialists
- See sample materials in action
- Receive a customized implementation proposal
Contact us today to learn how Soabar’s trolley identification solution can enhance your distribution center efficiency and sustainability.