Most Common Thermal Printer Faults and How to Resolve Them
Posted on 03/07/2017 in Company News, by Jon
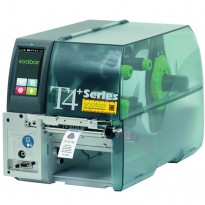
The Ultimate Guide to Troubleshooting Thermal Printer Issues
Why Thermal Printers Matter
Thermal printers are an invaluable asset for UK businesses seeking to create high-quality, durable labels while optimising operational efficiency and reducing costs. These versatile devices serve multiple functions across various industries, from retail and logistics to healthcare and manufacturing.
However, when printer faults occur, they can significantly disrupt your production and impact your bottom line. This comprehensive guide addresses the most common thermal printer issues faced by UK businesses and provides practical solutions to keep your operations running smoothly.
BUSINESS IMPACT: Studies show that printer downtime costs UK businesses an average of £120 per hour in lost productivity and delayed shipments.
Warning Signs Your Thermal Printer Needs Attention
Before we dive into specific faults, here are key indicators that your thermal printer may be experiencing issues:
- Declining print quality
- Incomplete label printing
- Faded or blurred text and barcodes
- Streaking or lines across labels
- Inconsistent printing results
- Unusual noises during operation
The 5 Most Common Thermal Printer Faults and Their Solutions
1. Dirt and Debris Accumulation
Problem: Thermal printers naturally generate and attract dust, dirt, and other contaminants. Without proper maintenance, these particles can clog your printer and print head, causing:
- Incomplete printing
- Missing elements on labels
- White lines across printed areas
- Premature wear of printer components
Solution: Implement a regular cleaning schedule using appropriate cleaning products:
- Clean your printer every time you change a label roll
- Use Soabar printhead wipes specifically designed for thermal printers
- Pay special attention to the print head, rollers, and paper path
- Remove loose debris with compressed air before wiping surfaces
UK Compliance Note: Regular maintenance helps ensure your printed barcodes meet GS1 UK standards for retail and supply chain applications.
2. Incompatible Ribbons and Materials
Problem: Using incorrect ribbon and material combinations often results in:
- Poor print quality
- Faded or smudged images
- Reduced label durability
- Excessive dirt buildup inside the printer
Solution: Select the appropriate materials for your specific application:
- Consider the environment where labels will be used (indoor/outdoor, temperature extremes, exposure to chemicals)
- Match ribbon type (wax, wax/resin, resin) to your label material
- Use high-quality supplies from reputable UK suppliers
- Consult with Soabar’s technical team for expert advice on optimal material combinations
3. Incorrect Heat Settings
Problem: Improper heat settings on your thermal printer can cause:
- Too high: smudged, blurred images and potential ribbon breakage
- Too low: faded, incomplete printing with poor durability
- Both: barcode scanning issues and compliance problems
Solution: Optimise your printer’s heat settings:
- Adjust settings according to the specific ribbon and material being used
- Start with manufacturer recommendations and fine-tune as needed
- Create and save profiles for different material combinations
- Test printed barcodes with verification equipment to ensure readability
Pro Tip: Keep a log of optimal heat settings for each material combination to ensure consistency across print jobs and operators.
4. Creased Ribbon Issues
Problem: Ribbons that become creased during printing cause:
- Diagonal streaks across printed labels
- Inconsistent ink transfer
- Wasted materials and increased costs
Common causes include:
- Uneven print head pressure
- Incorrect ribbon loading
- Misaligned printer components
Solution: Address creased ribbons promptly:
- Remove the current ribbon carefully
- Clean the print head thoroughly using Soabar printhead wipes
- Check for any obstructions in the ribbon path
- Reload the ribbon according to manufacturer instructions
- Ensure the printer is on a level surface
Technical Support: Contact Soabar’s technical department for guidance on proper ribbon loading techniques specific to your printer model.
5. Worn Print Head
Problem: Print heads have a finite lifespan and will eventually show signs of wear:
- Thin vertical lines on labels
- Inconsistent print density
- Declining overall print quality
- Incomplete character printing
Solution: When a print head reaches the end of its useful life:
- Contact Soabar’s technical team to arrange a replacement print head
- Consider keeping a spare print head in stock for critical operations
- Have the installation performed by qualified technicians
- Implement preventive maintenance to extend the life of the new print head
Cost-Saving Tip: Regular cleaning and proper heat settings can extend print head life by up to 30%, significantly reducing replacement costs over time.
Preventive Maintenance Best Practices for UK Businesses
To minimise downtime and extend the life of your thermal printer:
Regular Maintenance Schedule
- Daily: Visual inspection and removal of visible debris
- Weekly: Thorough cleaning of external components
- Monthly: Deep cleaning of internal components and print head
- Quarterly: Professional service by Soabar’s technical team
Essential Supplies
- Soabar printhead cleaning wipes (pre-coated with appropriate cleaning solution)
- Compressed air for removing loose debris
- Lint-free cloths for external cleaning
- Approved isopropyl alcohol cleaning solution (when recommended by manufacturer)
Staff Training
- Ensure all operators understand proper loading procedures
- Provide training on basic troubleshooting techniques
- Create clear documentation for common maintenance tasks
- Designate responsible personnel for regular maintenance checks
Conclusion: Maximising Your Thermal Printer Investment
Thermal printers represent a significant investment for UK businesses, and proper maintenance is essential to protect this investment and ensure consistent, high-quality output.
By addressing common faults promptly and implementing a preventive maintenance routine, you can:
- Minimise costly downtime
- Extend equipment lifespan
- Ensure compliance with UK labelling standards
- Maintain consistent print quality
- Reduce overall operational costs
Get Expert Support
Soabar’s dedicated technical support team is available to help with:
- Regular printer servicing and maintenance
- Supply of genuine printhead cleaning wipes
- Troubleshooting assistance for complex issues
- Replacement parts and consumables
Contact Information:
- Email: sales@soabar.co.uk
- Technical Support Hotline: 0116 2847003